From Prototyping To Mass Production
Vacuum Casting Services
Custom solutions for high quality prototypes and parts
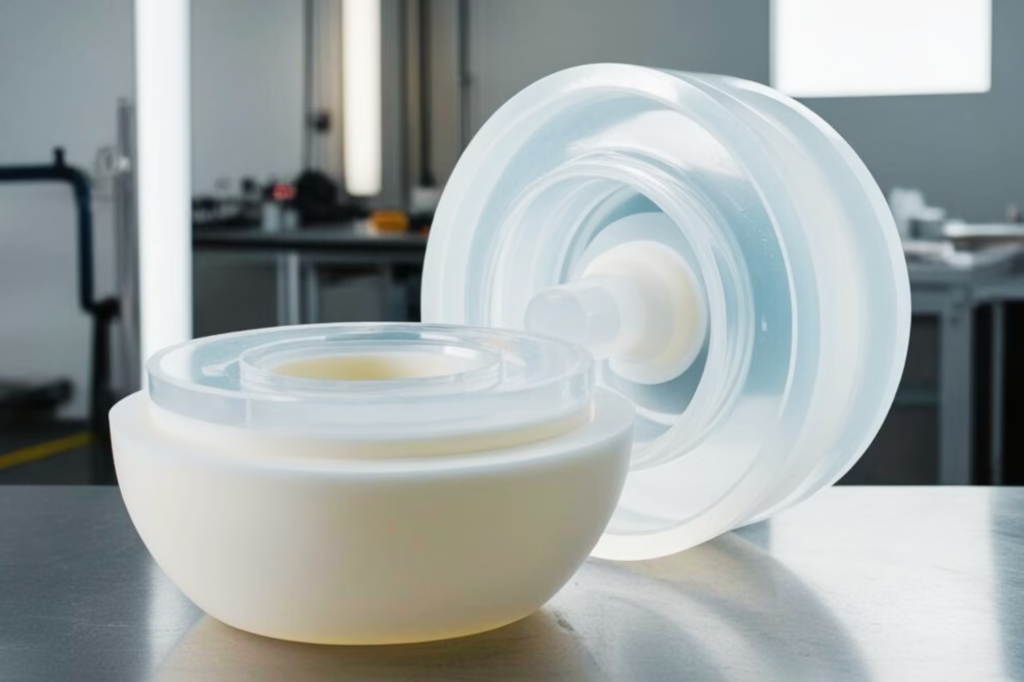
-
British, Danish & South African
Owned
-
ISO9001 & ISO13485
Certified
-
Full DFM & Global Technical
Support
-
No MOQ/MOV & Exceptional
Customer Satisfaction
Procision Vacuum Casting
What Is Vacuum Casting?
Polyurethane vacuum casting uses silicone molds and pourable polyurethane resins to make a limited number of copies of a master pattern. They have the look and feel of those made with plastic injection molding but at a fraction of the cost and lead time.
Procision Vacuum Casting
Advantages Of Vacuum Casting
- Fast, low-cost molds: Perfect for short runs, molds can be made in just days.
- Material versatility: Simulate the properties of common plastics like ABS, nylon, PP, acrylic, or soft TPE rubber, or opt for overmolding for multi-material solutions.
- Exceptional accuracy: Achieve highly detailed parts with excellent surface textures.
- Durable molds: Create 20 or more copies from a single mold, optimizing cost and efficiency.
- Flexible applications: Ideal for engineering models, rapid prototypes, samples, bridge-to-production parts, and end-use products.
When to Use Vacuum Casting?
Vacuum casting is the go-to solution when you need flexible, scalable manufacturing for small production without the cost or lead time of traditional tooling. Whether you’re validating a design with a prototype, preparing display models for a trade show or crowdfunding campaign, or transitioning to full-scale production, vacuum casting services deliver the performance and appearance of injection-molded parts — delivered faster and within your budget.
Materials
Your parts deserve vacuum casting materials that perform as well as they look. Vacuum casting resins closely mimic the properties of injection-molded plastics, including ABS, polypropylene, nylon, acrylic, and various hardnesses of soft elastomer. Add glass fibers for enhanced stiffness, or explore other finishing options to achieve the perfect result for your design.
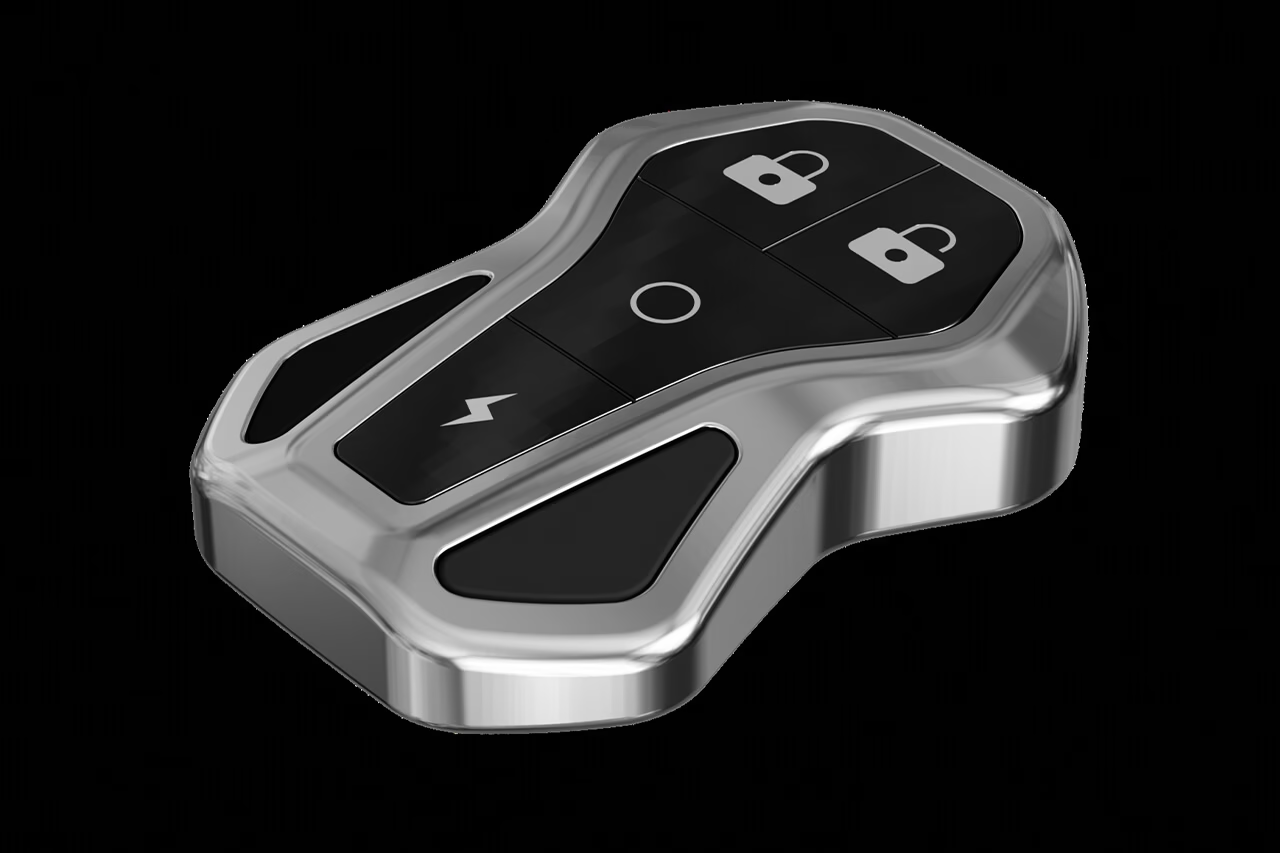
Why Choose Procision for Vacuum Casting Services?
When you partner with us for vacuum casting services, you’ll receive exactly the results you expect.
Exceptional Quality and Speed
Quality shouldn’t have to come at the expense of speed, and vice versa. When you partner with Procision Manufacturing, you can expect both. Your parts are crafted using the industry’s latest tools and techniques, and our typical lead time of 7–14 days for vacuum casting services ensures delivery on short timelines.
Finishing Services to Enhance Your Product
Go beyond casting with a wide range of finishing services. From machining and media blasting to painting and pad printing, you can enhance your parts to meet your exact specifications — all under one roof.
Smart Quoting and No Minimum Order Requirements
Why pay for more than you need? With no minimum order volume or dollar value, you get a service that adapts to your unique needs. And our smart quotation system delivers a detailed cost breakdown within 24 hours of your request.
Design for Manufacturing (DFM) Support and Remote Flexibility
If you’re finalizing your design, our experts are here to help. From creating master patterns to providing detailed DFM insights, we’ll guide you to a solution that works perfectly for your application. If you can’t visit us in person, we offer detailed video files showing all production steps.
Industry-Leading Material Verification and Quality Assurance
Controlled conditions throughout the process further guarantee precision, while Positive Material Identification (PMI) ensures full traceability and helps you meet regulatory requirements.
Ready To Start Your Project?
Are team of technical professionals are ready to assist.
Vacuum Casting Process
Creating high-quality polyurethane vacuum cast parts involves three critical steps: making the master pattern, crafting the molds, and casting the parts.
Step 1 : Creating Master Patterns
The master pattern is a 3D representation of your CAD design, often made through CNC machining or 3D printing methods like SLA/SLS. These patterns must withstand heating to 40°C to ensure optimal performance during the process. You can provide your own pattern, or skilled experts can create one tailored to your specifications.
Step 2 : Making the Molds
Liquid silicone is used to create molds that capture every detail of the master pattern. The process begins by meticulously sanding and sealing the pattern to ensure a flawless surface. Silicone is then poured around the pattern within a casting box and cured in an oven for 12-24 hours, depending on the size.
Step 3 : Casting Copies
With the mold prepared, your choice of casting resin is poured into the empty cavity under vacuum, ensuring precise replication of the master pattern. If needed, two or more materials can be overmolded for added functionality.
Common Questions
Procision Vacuum Casting Service FAQ
What makes Procision’s vacuum casting service unique?
Vacuum casting combines advanced techniques and premium materials to rapidly deliver prototypes and small production runs that look and feel like production parts. Complementary finishing options, like machining, painting, media blasting, and printing, enhance the final product even further.
Can Procision provide design services, industrial design support or product development support as an extension of its vacuum casting services?
Yes. Vacuum casting is often used for prototypes, and your design may still be evolving. DFM support for all incoming RFQs ensures your designs are optimized, with light assembly services available to streamline the process.
What are Procision’s quality standards for its vacuum casting services?
Every step of the vacuum casting process is governed by rigorous quality control. Materials undergo verification and testing before production begins, while conditions such as temperature and humidity are meticulously managed to ensure consistent results that meet the highest quality standards.
How do I get a quote for Procision’s vacuum casting services?
Getting a quote is simple. Upload your project details and optional CAD files to receive a free quote. With our smart quotation system, which is always verified by a human vacuum casting expert, you will receive an accurate and detailed quotation within 24 hours.