Engineering Excellence
CNC Milling Services
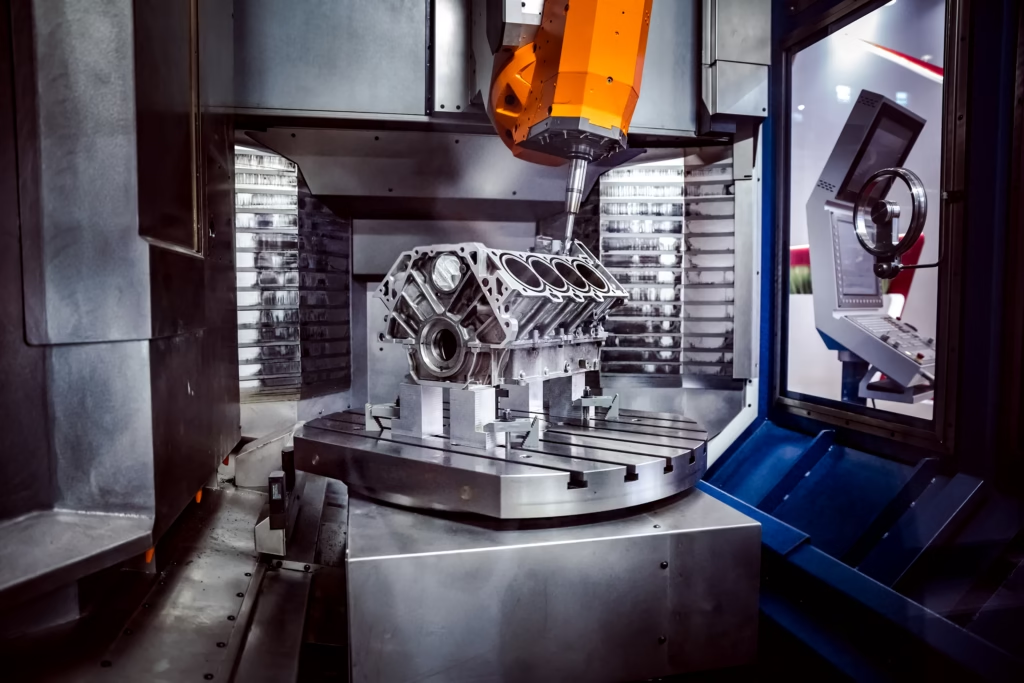
-
British, Danish & South African
Owned
-
ISO9001 & ISO13485
Certified
-
Full DFM & Global Technical
Support
-
No MOQ/MOV & Exceptional
Customer Satisfaction
- Total Projects
For more than 10 industries
- CNC Milling Centers
Multi-axis imported
- CNC Materials
To choose from
- Service Satisfaction
Based on yearly surveys
Procision Manufacturing
Custom CNC Milling Service
Procision CNC milling services are designed to blend cutting-edge technology with hands-on expertise. We combine multi-axis CNC milling machines with advanced software to fabricate end-use, tight tolerance parts suitable for any application.
We’re more than just a service provider. We’re an extension of your product development team. By deeply understanding your unique requirements, we deliver custom manufacturing solutions that go beyond the norm.
Procision Manufacturing
CNC Milling Explained
CNC milling is a subtractive manufacturing process that uses rotary cutting tools to selectively remove material from a solid workpiece. A 3D design model is created first, and that’s used to make a cutting program that guides the precise movements of the machine tool.
Our multi axis milling centers are both stable and flexible, enabling the workpiece to rotate at various angles while holding tight tolerances. This increases the types of features we can make in a single set-up, saving valuable time and money while ensuring high-quality, sophisticated designs for advanced applications.
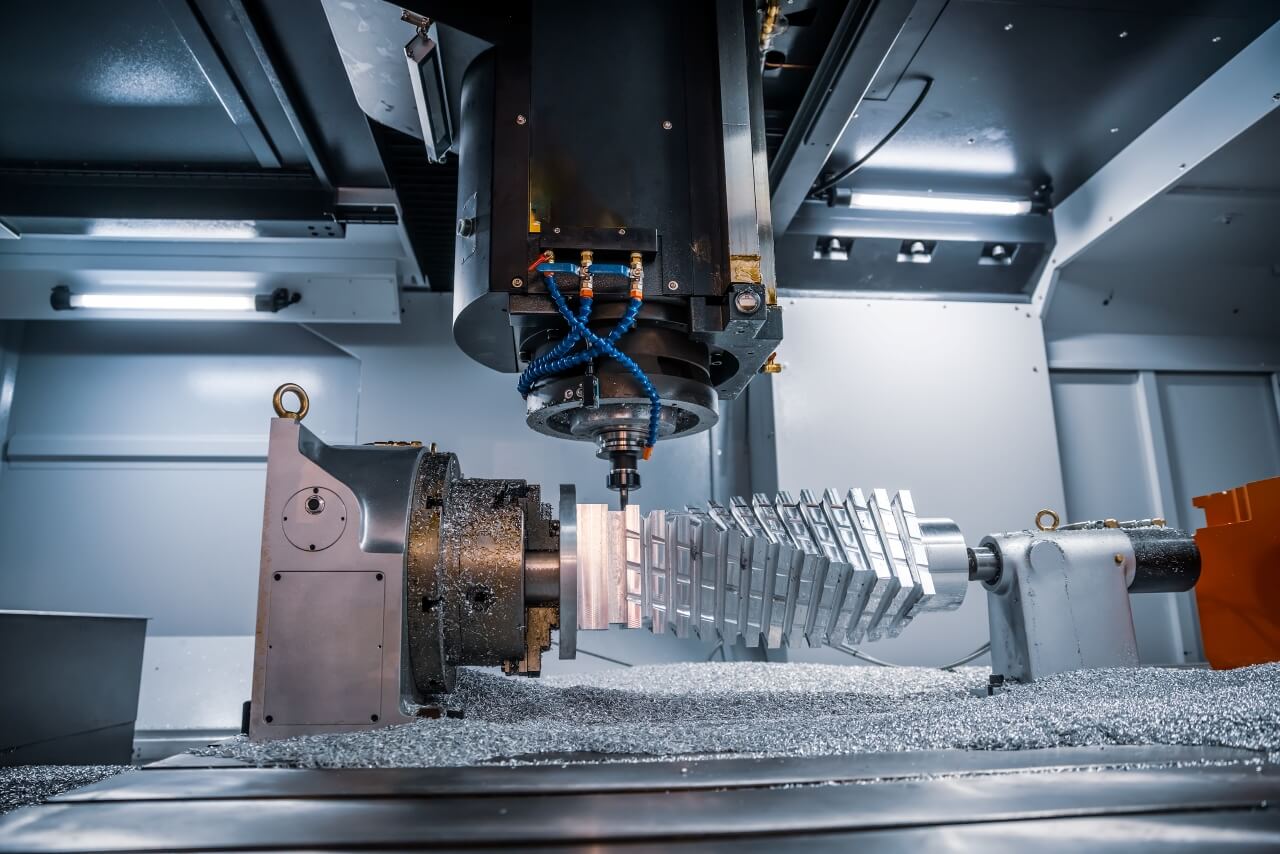
Procision Manufacturing
Why Choose CNC Milling Services?
CNC milling offers numerous benefits that make it the preferred choice for custom parts: fast, versatile, accurate, and repeatable. It can scale from a single prototype to unlimited mass production without the need for specialized tooling. The ability to create prismatic 3D shapes, contours, pockets, angled faces, ribs, and other intricate features in a single set-up ensures optimal efficiency. With tolerances down to a few microns, the finished parts are of full strength and ready for service with minimal post-processing.
At Procision, relentless improvement is at the heart of our services. We continually refine our processes, ensuring that we deliver high-quality parts with the accuracy and consistency that our clients depend on.
Procision Manufacturing
Materials for custom CNC Milling
- Metals: Aluminum, titanium, mild and stainless steels, copper, brass, magnesium, and more.
- Plastics: Rigid engineering resins like acrylic, nylon, ABS, PEEK, PTFE, etc.
- Composites: Carbon fiber, fiberglass
We’re committed to helping you make informed material choices. That means we provide you with clear, actionable insights about material suitability, ensuring you can innovate with confidence.

Ready To Start Your Project?
Are team of technical professionals are ready to assist.
Why Choose Procision Manufacturing?
We are committed to relentless improvement, continuously refining our CNC milling process to deliver even greater precision, efficiency, and quality. By combining innovation with purpose and a dedication to collaborative problem-solving, we ensure that every project is tailored to your specific needs and achieves exceptional results.
Premium Tools and In-House Machines
To deliver the highest quality results, we use advanced 5-axis CNC milling machines paired with premium cutting tools. This combination guarantees consistent accuracy for even the most intricate designs, demonstrating our relentless improvement in tooling and technology.
Expert Craftsmanship
Our skilled machinists work in tandem with our international engineering team to ensure your CNC milling parts meet and exceed the highest standards of performance. We’re committed to excellence without compromise in every aspect of our craftsmanship.
Transparent Quotations
We provide clear, detailed quotations with no hidden costs. Our pricing structure ensures full transparency, giving you a precise breakdown of material, machining, and finishing costs.
Certified Environment
ISO certified quality management and a clean climate-controlled facility ensure your parts meet stringent quality standards. We are certified to ISO 9001:2015, ISO 13485:2016 standards.
DFM (Design for Manufacturing) Review
Material and Quality Inspection
Worldwide Delivery
Common Questions
CNC Milling Services FAQ
Find answers to common questions about our CNC milling services and how we help industries like medical, electronics, agriculture, and consumer products achieve their goals.
What's the difference between CNC milling and turning?
Broadly speaking, in CNC milling, the workpiece remains stationary while the cutting tool rotates to remove material. This is best for creating flat surfaces, cavities, and prismatic shapes. In contrast, CNC turning rotates the workpiece while a stationary tool removes material, best suited for cylindrical features. Hybrid machines that combine both CNC milling and turning offer enhanced flexibility for complex projects.
What are the advantages of CNC milling vs 3D printing?
While both CNC milling and 3D printing are powerful manufacturing processes, they serve different purposes. CNC milling produces near-net final shapes that are ready to be used, offering precision and dimensional stability. It’s best for producing features that are in line-of-sight of the cutting tool. 3D printing, however, excels at making complex, hard-to-machine shapes that are not limited by line-of-sight. It’s also slower, less precise, and requires significant post-processing.
CNC milling works with a broader range of materials, including sheet metal and engineering plastic. CNC milling machines can also accommodate larger part sizes.
What are the tolerances of Procision's CNC milling service?
Our standard tolerances for precision CNC milling comply with ISO 2768-1 fine. This corresponds to +/- 0.05 mm deviation from the nominal, which is more than good enough for most projects. If you need even more accuracy, contact us to discuss our specialized service for precision components.
What materials can be used in precision CNC milling?
- Metals: Aluminum, mild and stainless steel, titanium, brass
- Plastics: Acrylic, PEEK, PTFE
- Composites: Custom composite materials
The choice of material depends on the application, mechanical requirements, and cost considerations. –
What industries benefit from CNC milling?
- Medical
- Electronics
- Consumer Products
- Aerospace
- Automotive
- Oil and Gas
Any industry requiring high-strength, tight tolerances, and customization can benefit from our CNC milling services.
What are the advantages of CNC milling?
- Accuracy: Achieves tight tolerances that are more than adequate for most common applications.
- Repeatability: Reliable, consistent results even in high-volume production.
- Surface finishes: Superior surface quality that’s ready for final finishing treeatments.
- Flexibility: No need for dedicated hard tooling; it’s easy to adapt to different designs and prototypes.
- Scalability: Whether you need a single part or one million, CNC milling works efficiently at any scale.
Our team is committed to delivering excellence without compromise, ensuring every part meets the highest standards for both prototypes and finished production parts.
What are the limitations of CNC milling?
While CNC milling excels at shaping flat surfaces, cavities, and intricate geometries, it is less efficient for creating cylindrical parts. These are better suited for CNC turning. Additionally, complex designs with deep cavities or thin walls may require specialized tooling or additional processing steps.
What types of parts can CNC milling create?
- Prototypes
- Molds
- Jigs and fixtures
- Enclosures
- Custom components with intricate designs
It’s particularly effective for parts requiring close tolerances and repeatable results.
What are common surface finishes for CNC milling parts?
- Media blasting
- Anodizing
- Chrome plating
- Powder coating
- Painting
- Polishing for a smooth surface
These finishes are designed to improve both the aesthetics and performance of your parts.
How do I get a CNC milling quote?
To request a CNC milling quote, simply submit your 3D CAD files along with project details, including material type, part quantity, color preferences, surface finish requirements, and any additional project specifications.
Our engineering specialists will evaluate your design for manufacturability and provide an accurate quotation within a few working days.
Common Questions
CNC Milling Services FAQ
Find answers to common questions about our CNC milling services and how we help industries like medical, electronics, agriculture, and consumer products achieve their goals.
How does CNC milling differ from CNC turning?
Each of these two CNC machining services has strengths and weaknesses. CNC milling uses a stationary workpiece and a rotating cutting tool to remove material, making it suitable for creating flat surfaces, cavities, and prismatic shapes. In contrast, CNC turning rotates the workpiece while a stationary lathe removes material, which is best for cylindrical parts.
How does CNC milling compare to 3D printing?
These two manufacturing processes differ significantly and cater to different aspects of product development. CNC milling can make near-net final shapes that are ready to be immediately put into service. However, it can only produce features that are in line-of-site of the rotary cutting tool. 3D printing is not limited to line-of-site features so it excels at making complex, hard to machine shapes. But it’s much slower and the dimensional accuracy is poor.
CNC milling works with a broader range of materials, including sheet metal and polymers like polyethylene and PMMA, ensuring superior mechanical properties and finishes. Milling machines can also accommodate larger part sizes with higher dimensional stability. On the other hand, 3D printing excels in producing intricate designs without the constraints of tool access, though the finish quality will require additional post-processing.
What materials can be used in CNC milling?
CNC milling supports a wide range of materials, including metals (aluminum, stainless steel, titanium, brass), plastics (acrylic, PEEK, PTFE), and composites. The choice of material depends on the application, mechanical requirements, and cost considerations.
What industries benefit from CNC milling?
CNC milling is used in industries such as medical devices, electronics, consumer products, aerospace, and automotive. It’s ideal for creating precision parts like medical implants, circuit boards, engine components, and custom housings with tight tolerances.
What are the advantages of CNC milling?
CNC milling is renowned for its high precision, repeatability, and ability to create parts with precise dimensions and superior surface finishes. Cutting programs can be set up quickly, while there’s no need for dedicated hard tooling. Also, CNC milling works just as well for a single part as for one million, so there are no volume restrictions.
The inherent flexibility and versatility of CNC milling makes it the single fastest way to make the widest variety of finished shapes from hard metals and plastics. These parts are full strength and can be used for prototypes and product testing as well as finished production parts. And CNC milling offers tight tolerances that are more than accurate enough for the vast majority of common applications in many industries and working environments.
What are the limitations of CNC milling?
While CNC milling excels at shaping flat surfaces, cavities, and intricate geometries, it is less efficient for creating cylindrical parts, which are better suited for our CNC turning services. It’s important to note that complex designs with deep cavities or thin walls may require specialized tooling or additional processing steps.
What types of parts can CNC milling create?
CNC milling can create a variety of custom parts, including prototypes, molds, jigs, fixtures, enclosures, and custom components with intricate designs. It’s particularly effective for parts that require close tolerances with repeatable results.
What are common surface finishes for CNC milled parts?
CNC milled parts can have finishes such as bead blasting for a matte look, anodizing for corrosion resistance, powder coating for durability, or polishing for a smooth surface. These finishes enhance appearance, functionality, and longevity.
How do I get a CNC milling quote?
To request CNC milling quote, submit project details including material, number of parts, color, surface finish, and anything else you want us to know about the project, along with optional 3D files. Engineering specialists will evaluate your design for manufacturability and provide an accurate online quote based on the complexity, material, and production needs.
Let’s Build What’s Next — Together
We are dedicated to continuously improving the level of our service to ensure your complete satisfaction. Whether you’re ready to submit a request for a quote (RFQ) or would like to explore your options further, we’re always here to support your custom cnc milling projects.