Many people seem to believe that CNC machining is the next big thing in the manufacturing industry. Actually, CNC machining has been around since the late 1970s, and by the mid-80s it began to gradually equal, and then replace, traditional machining for mass production. In fact, the market for CNC machining services has been steadily growing for more than 40 years. As of 2024 it had a global valuation of approximately $67 billion, which is forecast to reach $100 billion by 2034.
This impressive growth is due to several advantages it has over other mass production techniques like plastic injection molding. Today we’ll explore what CNC machining is, why it’s become so successful, and the secret to getting the most out this process when developing custom product designs.
What is CNC Machining?
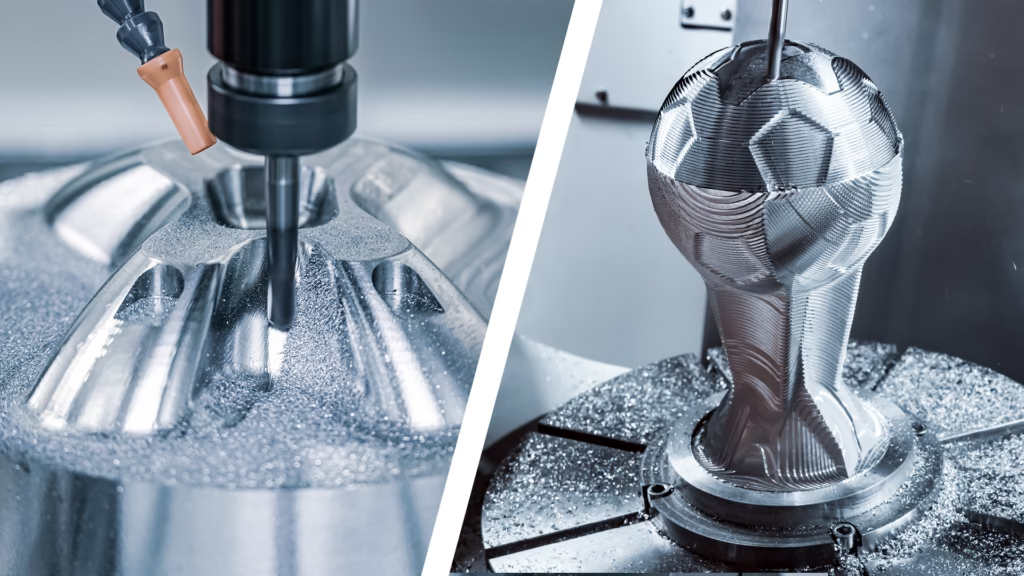
CNC machining is a broad category of related subtractive manufacturing processes for selectively removing material from a workpiece, where the movements of the machine tool are controlled by digital software. Contrast this with traditional machining, where the tools are controlled by skilled technicians operating levers, wheels and gears. These are impressive and valuable skills to be sure, but they aren’t able to meet the demands of high-speed modern production of consumer and industrial goods.
Common machine tools include CNC milling centers, CNC turning centers (or lathes), routers, grinders, and wire and sinker electrical discharge machines (EDM). There are also hybrid machines that combine two or more of these functions together, blurring the distinctions between them.
What is CNC milling?
In CNC milling, the workpiece is held in a vice or fixture on a worktable. Cutting tools of many shapes and sizes can then be mounted inside a spindle that rotates at high speeds. The rotating tool removes material from the workpiece at various angles while the workpiece is held rigid. It’s also common for the worktable to move relative to the axis of the spindle, which gives more options for making complex shapes.
CNC milling is best for making flat surfaces, prismatic shapes, slots, chamfers, pockets, and contours.
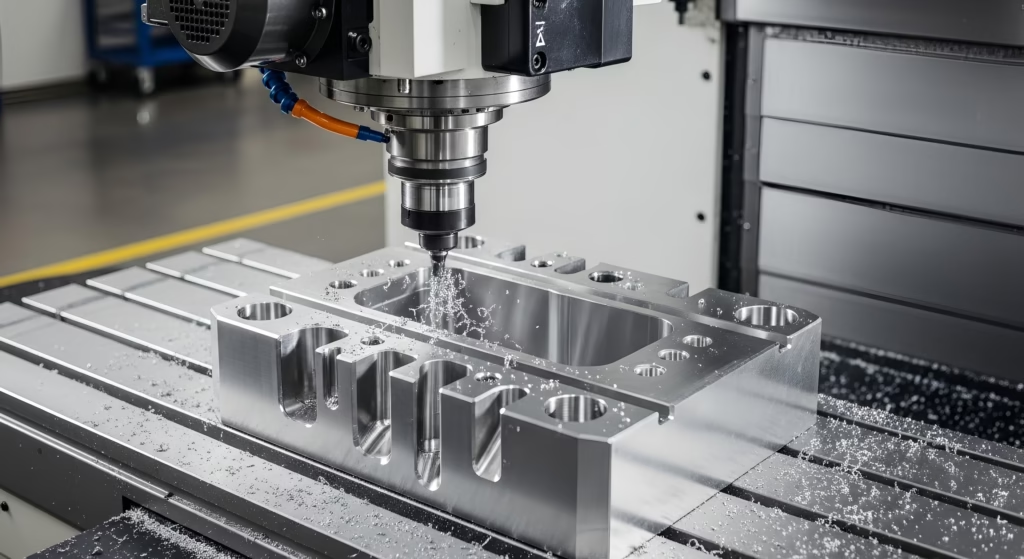
What is CNC turning?
In CNC turning, the workpiece is rotated relative to a stationary cutting tool. This allows for rapid removal of material and is excellent for making round and cylindrical shapes, bored holes, threads, and other circular features.
What is Sinker EDM?
Sinker EDM is also a subtractive machining process but it works on a different principle. It’s primarily used to erode the internal cavities of semi-hardened steels used for plastic injection molding.
Conductive electrodes of graphite or copper alloy are fabricated in the image of the desired final shape. These electrodes are sunk into a bath of dielectric fluid along with the workpiece. A powerful electrical current passes between the two conductors and, when it reaches a critical energy potential, a very hot plasma discharge erodes the surface in the shape of the electrode.
EDM is able to machine any conductive material. It produces tight tolerances with excellent surface finishes, and can also machine internal right angles impossible to do conventionally.
What is Wire EDM?
Like sinker EDM, wire EDM employs an electrical conductor, this time in the form of a thin copper wire mounted on a spool. This wire is able to easily cut through hardened steels so it’s a fast and efficient way to cut raw material to the desired external dimensions. However, it doesn’t work for internal cavities.
Why does CNC machining work so well?
CNC machines are able to achieve their impressive performance due to a couple of factors. First, they must be stable and rigid enough to hold consistent tolerances throughout their range of motion. They must also resist the undersirable influence of heat, humidity, and external vibration.
Sophisticated CAM (computer aided manufacturing) programs are used to develop ideal cutting parameters based on the part’s specification, tolerance, raw material and other factors. This software works with computer controls to ensure the machine follows each parameter the same way every time for maximum consistency.
This performance is further enhanced with sensors that constantly monitor and adjust the location of the cutting tool to sub-micron levels of accuracy. There are other technologies, always being developed and refined, that push the performance and reliability envelope even further.
When operated properly, CNC machine tools are capable of making strong, lightweight parts featuring tight tolerances and excellent surface finishes needing little or no post-processing. Such parts are often used in demanding industries like aerospace, automotive, oil and gas, agriculture, robotics and medical devices, to name but a few.
Regardless of the type of machine or the application, there are six fundamental benefits of CNC machining for custom part manufacturing that make it so valuable. Product developers should bear these in mind when considering their next project.
The Top Seven Advantages of CNC Machining
Speed
Compared to traditional machining there’s no contest. Modern machine tools, driven by digital control software and efficient brushless DC motors, are much faster to set-up and operate than their analog counterparts. When paired with high quality cutting tools, CNC milling and turning can be a perfect complement to rapid prototyping services when you want to get a physical sample fast.
Price
The price of a finished part is made up of fixed and variable costs added together. For example, you must pay for raw material based on the market price and there’s no way to change that. But there are ways to achieve cost savings by reducing variable costs like labor, tooling, and production times.
Fortunately CNC machining is not labor-intensive, it’s fast to set up and there is no fixed tooling in most cases – all of which saves money. And not only is machining fast, but it’s also consistent.
That last point is critical, because it’s consistency – not just maximum top speed – that helps manufacturers accurately predict and control production lead times to achieve sustainable throughput and cost savings.
Accuracy and Precision
These terms are closely related but not exactly the same. Accuracy, from a machinist’s point of view, means how close a measured value is to an exact specification. Precision, on the other hand, refers to how well a machine can achieve an accurate result, over and over again. It’s a measure of repeatability, very important when considering mass production volumes spread out over a long time.
Luckily, CNC milling and turning machine centers are both accurate and precise. This leads to better quality parts with tighter tolerances, and that means higher levels of performance and fewer defects.
Efficiency
Once a 3D CAD design has been programmed into a CNC machine, a near-net finished part can be made in a few minutes. After it has been measured and qualified, full production in any volume can proceed right away.
There is relatively little material waste or scrap, as would be the case with injection molding. And many CNC milling and turning operations also don’t need specialized fixed tooling, again representing efficient production and cost reduction. Because there is no fixed tooling, making a single part represents the same initial investment as making unlimited high volumes.
Versatility
CNC milling and turning machines are almost indifferent to the kinds of raw materials they can work with, provided the material is rigid enough to withstand the heat and pressure of the cutting tool.
There are caveats, of course. Magnesium, for example, is potentially combustible and so it must be machined using specialty cutting fluids to control the influence of oxygen on the magnesium dust. However, as exotic new materials like super alloys and advanced ceramics come onto the market, new milling and turning tools and techniques are being introduced to meet the challenges of the most demanding and hard-to-machine raw substrates.
Complexity
More and more CNC milling and turning centers are being built with additional axes of motion to perform complex operations in a single set-up. In many machine shops 5 axis mills are quite common, and CNC swiss lathes with live tooling and sub-spindles often operate in the 7–9 axis range.
This means that sophisticated shapes can be made without needing to dismount the workpiece from a holding fixture – always a potential source of induced errors in tolerance and accuracy. Such machines may cost more up front, but they pay for themselves with reduced downtimes and higher production efficiency.
Safety
Automated machine tools can be operated at the touch of a button while the workpiece is in a protective booth. The technician is therefore shielded from any moving parts or metal scrap. In addition, waste material and cutting fluid can be flushed away, filtered, and recycled. This protects the worker’s health and keeps the general environment cleaner and safer as well.
Furthermore, operators avoid the strain, fatigue and potential injury that comes from manually aligning and adjusting a variety of control wheels as they would with traditional machining. And all modern machines have a variety of passive and active systems designed to prevent any exposure to the dangers of a moving cutting tool.
Taken together, these seven advantages – speed, cost, accuracy and precision, efficiency, versatility, complexity, and safety – clearly demonstrate the many outstanding reasons why CNC milling and turning is such an ideal method for making a wide range of high quality finished parts.
Are all CNC machining services alike?
Does that mean that every factory with a CNC milling or turning center is able to produce components as quickly, efficiently, or on-spec as any other? Does simply having a machine and pushing a few buttons guarantee a satisfying result?
By no means, and that’s the difference between an average service provider and an exceptional one. Even the finest and most expensive equipment will deliver poor results if it’s not operated properly by skilled machinists who are able to make careful adjustments based on experience and careful attention to every detail.
The machine and the craftsman must therefore work seamlessly together to produce superior results. That’s what you can expect when you contact Procision Manufacturing for custom fabrication of advanced metal, plastic and composite rapid prototypes and production parts.